Food Trade and Chefs Uniform Laundry Process
Posted on May 24, 2022
In this video we guide you through our ISO 9001 Quality Management Certified laundry process at our Cheltenham laundry where the uniforms are scanned and tracked throughout the process. Firstly, all the uniforms returned by our customers are scanned to register that they have been returned to the laundry at this stage they are also sorted, checked for any damage that might need repair and any foreign objects are removed. The next stage is washing where full thermal disinfection is carried out to remove any dirt, bacteria or viruses that could be present, before transferal to our high care facility. This is where a second scan and quality check takes place before the finishing process where drying and further thermal disinfection take place. Any damage that has been reported, either by customers before being returned to the laundry or identified at the laundry, undergoes stringent inspection. Depending upon the findings of the inspection, garments are either repaired, damaged labels replaced or garments are removed and replaced with new garments.
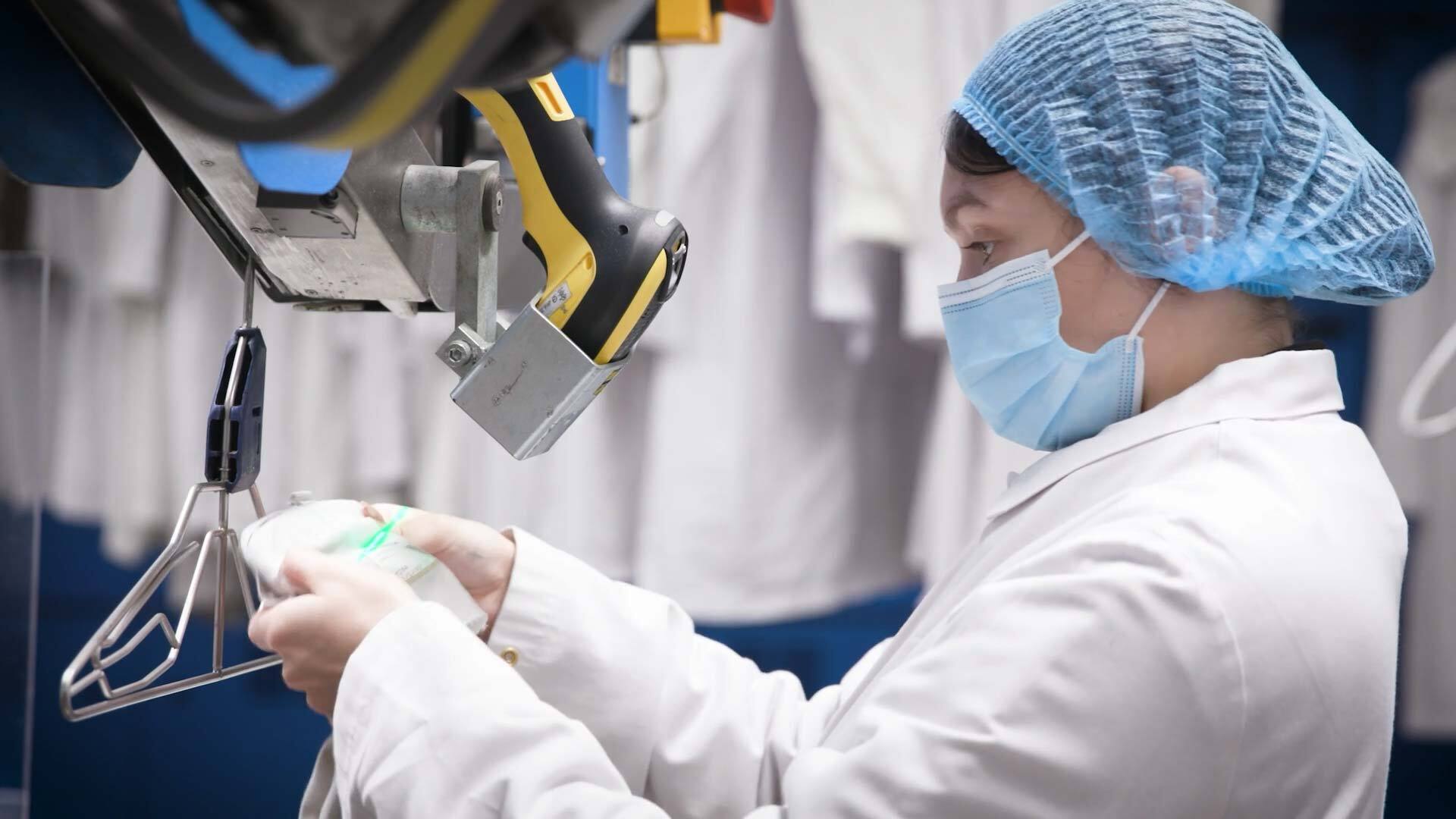
Once the uniforms have passed the inspection process or have been repaired, they enter the automated sorting system, where they are sorted according to the customer's needs. Each customer will have their own packing requirements to ensure simple distribution at their premises. For example, they may have garments sorted by type, colour and size or into sets for each wearer before delivery to an individual employee locker. Once everything within an order is sorted the uniforms are neatly folded and packed ready for dispatch to our customers.
To find out more about how CLEAN can help you ensure your employees have a regular supply of clean, smart, branded garments or uniforms that are cleaned on a reliable, regular schedule, visit cleanservices.co.uk/workwear, email info@cleanservices.co.uk or call 0330 818 7008
Video
Share this page:
Share