Quality, professionalism and service. That is the CLEAN imperative as we embark on the next steps of our world-class manufacturing journey which will see our new super laundry open later this year.
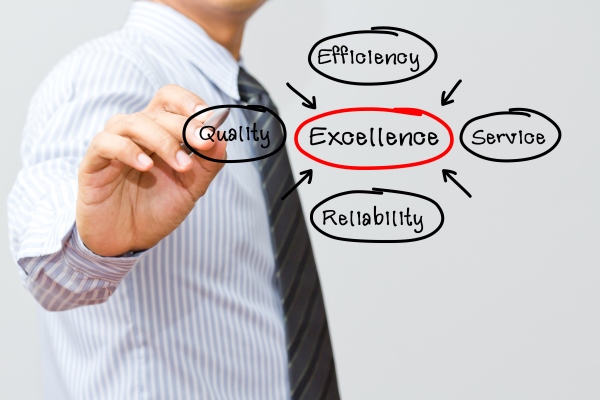
The site in Slough has been custom designed in collaboration with Kannegiesser, one of Europe’s largest suppliers of high-quality laundry machinery, and will be the most technically advanced in Europe and beyond. As well as embracing environmental considerations, focusing significantly on the optimisation of energy and chemical consumption, the site’s design means we can provide our customers with superior service.
Everyday Excellence
Our operational platform is changing and customers are at the heart of this journey. My philosophy is that to grow strong you need solid foundations. The five pillars in the CLEAN Operational Excellence Strategy are: Customer Loyalty, People, Supply Chain, Plant and Equipment, and Continuous Improvement. These are our base building blocks upon which we can create a world-class tomorrow that is changing the face of our business and the laundry industry as a whole.
The new CLEAN is committed to delivering Everyday Excellence. Our Customer First company culture means that Operations and Commercial work seamlessly together for one agenda – to deliver exceptional, unrivalled customer service the CLEAN way.
STOP
We employ more than 1,400 people across 10 sites in the UK. The health, safety and wellbeing of our people is our highest priority and ‘protecting people from harm’ is a mantra that is part of CLEAN’s DNA.
This relentless approach to excellent health and safety practices is demonstrated through the implementation of the STOP (Safety, Total, Observation, Process) programme that was spearheaded by CLEAN’s chief operating officer Bob King. The STOP programme is led by general managers of each site and involves walking the factory floor to identify and resolve any hazards that may pose a risk to harm. To date we have identified and prevented well over 1,000 actions that could have caused an accident or injury and will continue this process every week.
Everything Can and Should Improve
Across our business continuous improvement is now the norm because we make it a habit by following some simple but incredibly effective approaches:
1. Not a single day should pass without some improvement being made
2. Imagine the ideal customer experience and strive to provide it
3. Don’t criticise, suggest an improvement
4. Think of how to improve it instead of why it can’t be improved
5. Think beyond convention, even if something is working, try to find ways to make it better
6. See problem solving as a cross-functional, systemic and collaborative approach
At CLEAN we follow three simple concepts, adapted from proven manufacturing techniques:
Gemba – Getting to the heart of and going to the problem. We cannot fix things from behind a desk.
Kaizen – Always striving for perfection and seeking to make every day processes better.
Top three – Focusing on the top three actions based on thorough analysis then applying ‘The Hundred Year Fix’.
Picture: Record Breakers at our Cheltenham Laundry delivering best ever results for the number of pieces processed per operating hour is evidence of Everyday Excellence in practice
Our business is changing for the better. All of our colleagues, from shop floor to top floor, are one CLEAN dedicated to providing a high quality product
delivering industry leading levels of customer service and supply that delight our customers. The road to Everyday Excellence is made up of many steps.
We want people to aspire to use our service and we are working together towards a brighter future, with the single vison of being the UK’s linen provider
of choice.
What can you do today, that will make tomorrow better than yesterday?
Ready to talk to us? Contact us today for a FREE no obligation quote.
Graham Paterson
Site Operations Director
CLEAN
Share this page:
Share